Why Tamahagane is Considered the Top Steel for Swords
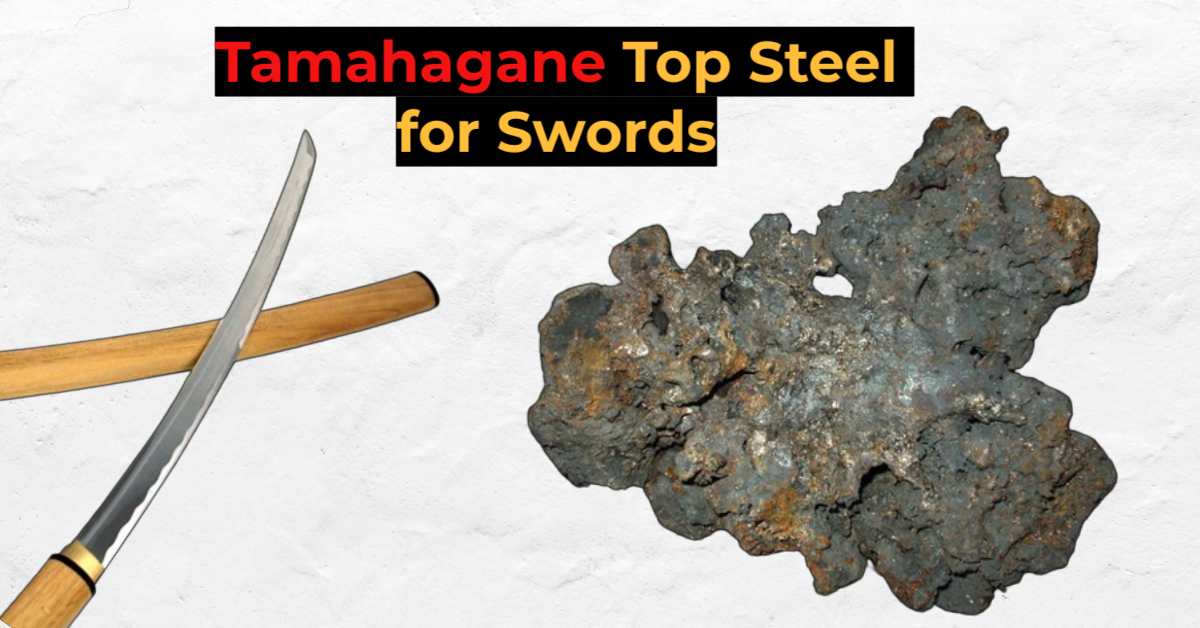
Discover the fascinating world of Tamahagane steel, a special metal deeply connected to traditional Japanese art and legend. This unique material has intrigued craftsmen and sword enthusiasts for generations, with a history rich in culture and mystery.
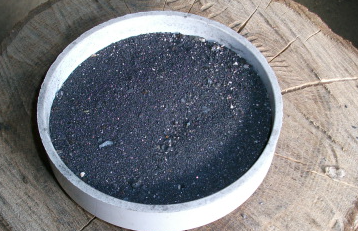
A bowl of satetsu or iron sand. Credit: Richard C. Shaffer
Japanese Samurai coveted Tamahagane steel for their swords. Swordsmiths meticulously experimented for years to create this superior metal.
But did they succeed?
This article will move beyond the myths and focus on the hard facts. Delve into Tamahagane Steel’s history, production process, and properties to determine if it remains the superior choice for crafting swords.
Tamahagane Steel – What Is It?
For centuries, skilled Japanese swordsmiths have crafted legendary Samurai swords using a unique steel called Tamahagane. This extraordinary material originates from Satetsu, a special iron sand found in abundance in Shimane Prefecture, southern Japan. To transform this iron sand into the prized Tamahagane, artisans employ a time-honored technique within a Tatara furnace – a historical marvel preserved for over a millennium.
The term Tamahagane translates to “precious steel,” with “tama” meaning precious and “hagane” meaning steel. There are two main types of Tamahagane steel: Masa Satetsu and Akame Satetsu. The difference between them lies in the amount of iron ore and carbon used in the steel, with Masa being of higher quality.
Historically, the Japanese struggled to find iron ore since many deposits are underwater around the archipelago. However, Japan has an abundance of volcanoes that produce basalt and granite rocks. Over time, these rocks break down into iron sand, which Japanese swordsmiths have used to create their renowned blades.
Transforming Iron Sand into Tamahagane: Japanese Blade Making Art
Japanese artisans have meticulously refined the process of transforming iron sand, sourced from rivers, coasts, and hills across Japan, into the legendary Samurai blades over countless generations. Here’s a look at the key steps involved in creating Tamahagane blades.
1. From Field to Forge: Collecting Iron Sand
People dig up silts from specific locations to obtain iron-rich river sand or dust. Subsequently, they meticulously wash and clean the collected material to eliminate impurities. This process continues until only the purest iron sand remains. Workers load approximately 25 tons of iron sand into a tatara, a rectangular clay furnace designed to produce Tamahagane steel.
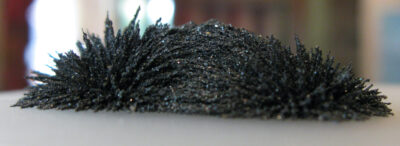
From Field to Forge: Collecting Iron Sand Image Credit: Wikipedia
Workers dismantle the tatara after every production run. To refine iron into various forms, it must be fully submerged in the furnace, where it settles at the bottom of the container.
2. The Art of Smelting: Transforming Raw Materials into Pure Metal
The tatara will be lit, reaching temperatures of up to 2,500 ºF (1400 ºC), reducing the iron ore to steel and yielding high quantities of Tamahagane. Traditional Sumi charcoal production methods create carbon-rich material. Tamahagane, a type of steel, can be refined into purer and less pure forms. The highest quality Tamahagane is a key ingredient for crafting exceptional swords.
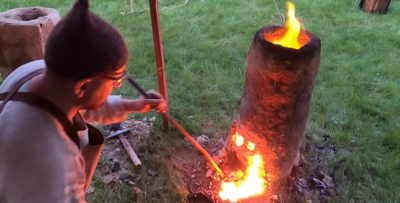
The Art of Smelting: Transforming Raw Materials into Pure Metal. Image Credit: officina ferraria
Blacksmiths intentionally prevent Tamahagane from reaching a molten state to precisely control its carbon content, maintaining a range of 0.5% to 1.5% for optimal blade properties. Two types of Tamahagane emerge from this process: high and low carbon. A master swordsmith, a murage, carefully combines two distinct metals to forge a samurai sword. Using only one metal would create a blade that is either too brittle or dulls quickly. The murage’s expertise lies in finding the perfect balance between these metals to produce a superior sword.
3. Removing Impurities: Techniques for Purifying Metal and Materials
A skilled swordsmith receives the finest Tamahagane steel and initiates the crafting process by repeatedly hammering, heating, and folding the steel. The sparks that fly during hammering indicate the presence of impurities, such as air bubbles, in the steel.
As the swordsmiths work, they remove slag, a byproduct of combining iron and carbon. The swordsmith carefully assesses the carbon concentration in the Tamahagane while continuously pounding and shaping the metal bar, ensuring the steel has the right properties for crafting a quality sword.
4. Forging the Sword: Techniques and Traditions of Blade Crafting
Once the impurities are removed, the precise forging of the Tamahagane sword begins. The swordsmith first shapes the high-carbon steel into a long, U-shaped channel. The core steel is then shaped to fit securely inside this channel.
The high-carbon Tamahagane forms the sharp, hard edge of the blade, while the core steel provides strength and durability. This careful balance is essential for crafting a high-quality Tamahagane Japanese sword. The “sandwich” of metals is then hammered and welded together, shaping it into a functional and sharp blade.
5. The Coating and Final Heating Process
A craftsman applies a mixture of clay and charcoal powder to the back edge and upper sides of the completed Tamahagane steel blade. This coating protects the sharp front edge and creates a distinctive Hamon design. The blade is then heated in the fire to a temperature not exceeding 1,500°F (815°C).
6. Mastering Shaping: Techniques for Crafting Perfect Metal Forms
Craftspeople shape the blade’s curve by rapidly cooling it in water after the final heating process, a technique called quenching. This step is crucial but can sometimes affect the quality of the Tamahagane steel.
The distinctive curve arises due to the different carbon levels in the Tamahagane. The back and inner core of the blade, which have less carbon, contract more freely than the higher-carbon front edge. The varying rates of contraction between these areas cause the blade to bend, giving it the signature Japanese curve.
7. Polishing Metal: Techniques for a Brilliant, Smooth Finish
With the Tamahagane blade fully forged and curved as intended, it is then sent to a skilled polisher. This expert uses water stones to refine the blade, a process that can take three weeks or more.
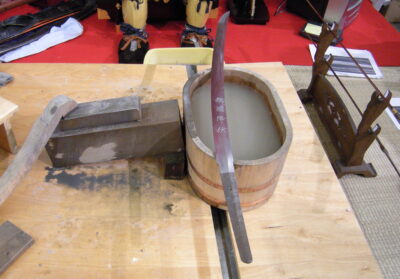
Polishing Metal: Techniques for a Brilliant, Smooth Finish. Image credit: Wikipedia
Water stones are prized possessions, often handed down through families. These costly stones, valued at over a thousand dollars, are made of clay embedded with hard silicate particles. Through the continuous process of rubbing and grinding, the clay wears away, gradually exposing more silicate particles. This unique composition allows for the creation of an incredibly fine, precise polish on the legendary Tamahagane blade.
8. Final Steps in Sword Crafting: Adding Parts
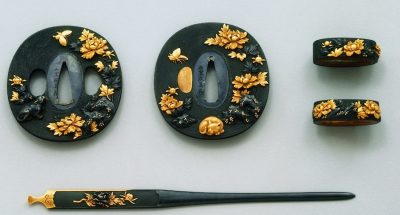
Final Steps in Sword Crafting: Adding Parts. Image Credit: Wikipedia
Another expert has now received the finished blade and will attach the final components: the guard, handle, scabbard, and additional decorative pieces. Assembling these parts can take up to six months and may require the efforts of more than 15 skilled craftsmen to complete a single high-quality Tamahagane sword.
How Much Tamahagane is Needed to Make a Katana?
Each Japanese Samurai sword requires different amounts and types of Tamahagane steel, carefully chosen by skilled swordsmiths through a detailed process. Only after this selection is the smelting of Tamahagane steel started.
The amount of Tamahagane needed depends on the length of the sword. For instance, a Katana—the most well-known Japanese sword, which sits between the shorter Tanto and the longer Odachi—typically requires between 22 to 44 lbs (10 to 20 kg) of Tamahagane steel. This amount can vary, depending on the craftsmanship and techniques of the blacksmiths.
A traditional Katana typically weighs around 2.2 lbs (1 kg), which might make you wonder about the rest of the Tamahagane steel. The weight of the initial Tamahagane block is not equal to the weight of the final blade due to the extensive forging process.
As mentioned earlier, the Tamahagane is folded repeatedly during forging. This process causes most of the steel to turn into iron oxide and removes many impurities, which results in the sparks seen around the blacksmith. Additionally, heat treatment affects the amount of Tamahagane needed; an experienced swordsmith can minimize the amount of steel lost to oxidation, thus affecting the final weight of the Katana.
Is Tamahagane Steel the Strongest Steel for Swords?
The Katana is one of the most famous swords in the world, often seen as a symbol of unparalleled strength and durability due to its steel. However, opinions on the Katana’s effectiveness vary widely. Some view it as a powerful weapon, while others see it as outdated and weak due to the use of Tamahagane steel. So, where does the true strength of Tamahagane lie?
The reality is somewhere in between.
Tamahagane steel is not the strongest or most advanced steel available. It doesn’t cut through every type of metal, nor is it the fastest, sharpest, lightest, or most flexible. It also doesn’t grant any magical powers or special aura. However, Tamahagane is a high-carbon steel that remains a respected and effective material for blades.
The belief in its extraordinary strength often comes from the myth that Tamahagane is folded over 1,000 times to achieve its legendary durability. In truth, research and testing show that Tamahagane steel’s strength does not significantly increase after the third fold. The actual number of folds used to shape a Tamahagane blade is usually no more than 20.
How Much is a Tamahagane Sword?
Although Tamahagane swords may not be as durable as modern steel swords, their intricate folding and forging process makes them highly prized. Even today, skilled artisans meticulously craft these swords using traditional techniques, resulting in each piece being a unique masterpiece. Authentic Japanese Tamahagane swords can cost over $3,000 and require more than 20 artisans, with production taking up to two years.
When searching for a Tamahagane sword, it’s important to ensure that it was made using genuine Japanese swordsmithing techniques. Although China and the United States have successfully replicated the Tamahagane swordmaking process, their products do not embody the authentic artistry and historical legacy of Japanese craftsmanship.
The process of making a sword from iron sand adds significant value. Investing in a Tamahagane sword is worthwhile only if it is crafted by a genuine Japanese swordsmith.